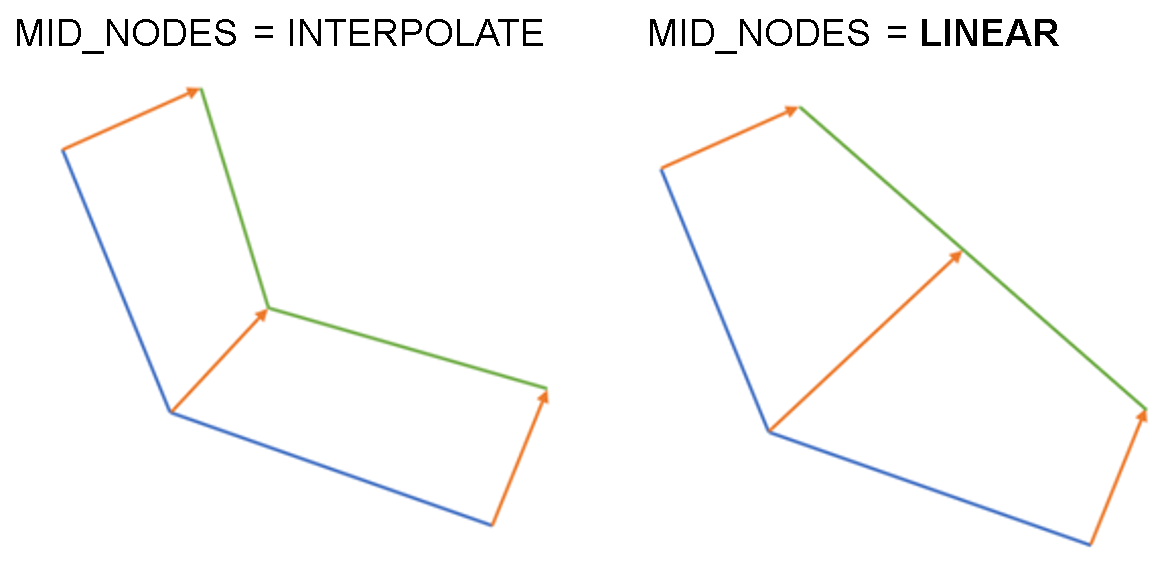
Strictly speaking, design variables are the signed amounts of optimization
displacement applied to the design nodes. In
unrestricted tasks, the direction of the optimization displacement vector
corresponds to the outer surface unit normal on the node and the amount
of displacement is determined by the optimization procedure. Restrictions
influence the amount and direction of the optimization displacement vector.
Basically there are three cases that might occur:
- Growth means that
a design node is moved outwards (positive amount of displacement).
- Shrinkage
means that a design node is moved inwards (negative amount of displacement).
- Neutral means that a design node is moved neither outwards nor inwards
(zero displacement).
Determination of Optimization Displacement Vectors
- The optimization displacement vector on the design node is determined
by superimposing all external element normal vectors on the boundaries
of neighboring elements. In two-dimensional models the normals are formed
relative to element edges and in three-dimensional to element surfaces.
The only element edges or element surfaces that are taken into consideration
are those spanning design nodes. Isolated
design nodes (neighboring nodes on the surface are not design nodes)
are not permitted and must be removed from the design node group. The
optimization displacement direction is a uniform vector.
Example:
In a two-dimensional model each design node has two neighboring
nodes on the boundary of the component. If both of these neighboring
nodes are design nodes, see the figure above on the left, two normal
vectors are formed, one each for the respective element edges, and superimposed.
If only one of the neighboring nodes is a design node, see the
figure above on the right, there is only one normal vector. This is identical
with the normal vector of the design node.
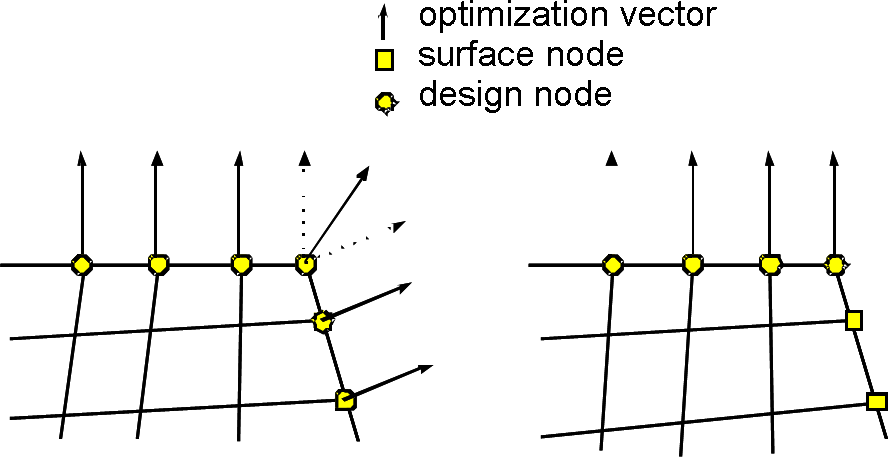
- If the displacement direction of a node is restricted
by a design variable constraint (
DVCON_SHAPE
), the direction of
the optimization displacement vectors is correspondingly adjusted.
- The optimization displacement vector is derived from scaling the
optimization displacement direction with the signed amount of displacement
calculated by the optimization procedure.
- The length of the optimization displacement vector might also be influenced
by design variable constraints (
DVCON_SHAPE
).
Note:
- The optimization displacement vector determined by the optimizer is
adjusted to the changed conditions in each design cycle (for example, shape of
the structure, effective restrictions, mesh quality, etc.). The optimization
displacement vectors are therefore not constant; they are subject to
certain changes in each cycle.
- With the
VECTOR
parameter in the
optimization settings (command OPT_PARAM
), it is
possible to control when the optimization displacement vectors are
calculated.
Supported Elements Attached to Shape Sensitivity Design Nodes Using SENS_CALC_MODE = SOLVER with
Abaqus.
Valid element types for sensitivity-based
nodal optimization with Abaqus sensitivities. |
Abaqus element type |
PLANE_QUAD_4 |
CPE4
CPE4R
|
PLANE_QUAD_4 |
CPEG4
CPEG4R |
PLANE_QUAD_4 |
CPS4
CPS4R |
PLANE_QUAD_8 |
CPEG8
CPEG8R |
PLANE_QUAD_8 |
CPS8
CPS8R
|
PLANE_QUAD_8 |
CPE8
CPE8R
|
PLANE_TRIANG_3 |
CGAX3
CGAX3H
CPE3
CPS3
|
PLANE_TRIANG_6 |
CPEG6
|
PLANE_TRIANG_6 |
CPS6
|
Valid element types for sensitivity-based
nodal optimization with Abaqus sensitivities. |
Abaqus element type |
SHELL_QUAD_4 |
S4
S4R |
SHELL_QUAD_8 |
M3D8
S8R |
SHELL_TRIANG_3 |
S3
S3R
|
Valid element types for sensitivity-based
nodal optimization with Abaqus sensitivities. |
Abaqus element type |
SOLID_BRICK_8 |
C3D8
C3D8R
|
SOLID_BRICK_20 |
C3D20
C3D20R
|
SOLID_TETRA_4 |
C3D4
|
SOLID_TETRA_10 |
C3D10
C3D10HS
|
SOLID_PENTA_6 |
C3D6
|
SOLID_PENTA_15 |
C3D15
|
Supported Elements Attached to Shape Sensitivity Design Nodes using SENS_CALC_MODE = TOSCA.
Valid element types for sensitivity-based shape optimization |
Abaqus element type |
ANSYS® element type |
MSC Nastran® element type |
Solid elements |
SOLID_TETRA_4 |
C3D4 |
SOLID285 |
CTETRA4 |
SOLID_TETRA_10 |
C3D10 |
SOLID148 SOLID187 SOLID92 |
CTETRA10 |
SOLID_BRICK_8 |
C3D8 C3D8R |
SOLID185 SOLID45 |
CHEXA8 |