ID_NAME |
= <id_name_of_link_shape > |
Name of LINK_SHAPE definition. |
MAIN |
|
Determination of the main node |
|
= MAX |
Maximum growth and minimum shrinkage. Allowed for all CLIENT types in controller-based shape optimizations. |
|
= MIN |
Maximum shrinkage and minimum growth. Allowed for all CLIENT types in controller-based shape optimizations. |
|
= NODE , <node_nr > |
Node <node_nr > is the main node. Only allowed for the following CLIENT types: PLANE_SYM POINT_SYM VECTOR DIRECTION LENGTH DISP_CS . |
|
= NDGR , <node_group> |
Main is determined from the nodegroup <node_group>. From each link-shape group, one node must exist in the main group.
Only allowed for the following CLIENT types:
PLANE_SYM ,
POINT_SYM ,
ROTATION_SYM ,
DIRECTION ,
DISP_CS ,
SURF_TURN ,
FREE_FORM VECTOR ,
LENGTH ,
SURF_STAMP (in case of shape sensitivity). |
|
= AUTO |
Tosca determines the best main criterion. Only allowed for the following CLIENT types:
SURF_TURN . |
CLIENT |
Determination rule for the client nodes: |
|
= PLANE_SYM, AXIS_1
= PLANE_SYM, AXIS_2
= PLANE_SYM, AXIS_3 |
A symmetrical displacement of the nodes referring to the plane that lies normal to the given axis of the coordinate system. |
|
= POINT_SYM |
A symmetrical displacement of the nodes referring to the origin of the coordinate system is enforced. |
|
= ROTATION_SYM, AXIS_1
= ROTATION_SYM, AXIS_2
= ROTATION_SYM, AXIS_3 |
A rotational symmetric displacement of the nodes referring to the given axis of the coordinate system is enforced. |
|
= VECTOR
= VECTOR,ON/OFF,ON/OFF,ON/OFF |
All displacement components are coupled. The choice of which components to couple and which not to couple is done using the
ON or OFF switch. The first switch controls the first component etc. |
|
= DIRECTION |
All displacement components are coupled. The resulting displacement vector is scaled to the original absolute value of displacement. |
|
= LENGTH |
Only the amount of displacement is coupled. |
|
= DISP_CS = DISP_CS,ON/OFF,ON/OFF,ON/OFF |
The displacement is coupled in the relevant displacement coordinate system. The choice of which components
to couple and which not to couple is done using the ON or OFF switch.
The first switch controls the first component etc. |
|
= SURF_STAMP, AXIS_1
= SURF_STAMP, AXIS_2
= SURF_STAMP, AXIS_3 |
Conserve a stampable surface. The stamping direction is defined by the axis of the coordinate system. |
|
= SURF_TURN, AXIS_1
= SURF_TURN, AXIS_2
= SURF_TURN, AXIS_3 |
Conserve a turnable surface. The rotation axis is defined by the coordinate system axis. |
|
= SURF_DRILL, AXIS_1
= SURF_DRILL, AXIS_2
= SURF_DRILL, AXIS_3 |
Conserve a drillable surface. The generated surface is demoldable and turnable. The drilling axis is defined by the coordinate system axis. |
|
= SURF_DEMOLD, AXIS_1
= SURF_DEMOLD, AXIS_2
= SURF_DEMOLD, AXIS_3 |
Conserve a demoldable surface for casting. The demold direction is defined by the coordinate system axis. |
|
Determination rule for the client nodes with CLIENT_DIR or DEMOLD_DIR parameter: |
|
= PLANE_SYM |
A symmetrical displacement of the nodes referring to the plane that lies normal to the axis specified by CLIENT_DIR . |
|
= ROTATION_SYM |
Conserve a rotational symmetric surface with rotational symmetric mesh. Symmetry groups are determined
automatically according to the axis specified by CLIENT_DIR parameter. |
|
= SURF_PLANE_SYM |
Conserve plane symmetry for nonsymmetric meshes. The symmetry axis is defined by CLIENT_DIR . |
|
= SURF_CYCLIC_SYM |
Conserve cyclic symmetry for nonsymmetric meshes. |
|
= SURF_CYCLIC_PLANE_SYM |
Conserve cyclic and plane symmetry for nonsymmetric meshes simultaneously. |
|
= SURF_STAMP |
Conserve a stampable surface. The stamping direction is defined by the CLIENT_DIR parameter.
An additional demold direction can be defined using DEMOLD_DIR . |
|
= SURF_TURN |
Conserve a turnable surface. The rotation axis is defined by the CLIENT_DIR parameter. |
|
= SURF_DRILL |
Conserve a drillable surface. The generated surface is demoldable and turnable. The drilling axis is defined by the CLIENT_DIR parameter. |
|
= SURF_DEMOLD |
Conserve a demoldable surface for casting. The demold direction is defined by the DEMOLD_DIR parameter.
(CLIENT_DIR is also supported, but not recommended). |
|
= FREE_FORM |
The node group referenced by MAIN=NDGR, < node_group> defines a free form surface;
Can only be used if this command is referenced by DVCON_SHAPE , CHECK_SLIDE . |
CLIENT_DIR |
= <x_1 >, <x_2 >, <x_3 > |
Direction of the axis for the restrictions PLANE_SYM, ROTATION_SYM, SURF_STAMP, SURF_TURN, SURF_DRILL,
SURF_DEMOLD, SURF_PLANE_SYM, SURF_CYCLIC_SYM, SURF_CYCLIC_PLANE_SYM with reference to the specified coordinate system. |
DEMOLD_DIR |
= <x_1 >, <x_2 >, <x_3 > |
Demolding direction for the restrictions SURF_STAMP and SURF_DEMOLD
(CLIENT_DIR also possible) with reference to the specified coordinate system. |
CS |
= <name_of_coord_system> |
Name of the coordinate system in which the link condition is defined (that is, which the axis or
CLIENT_DIR /DEMOLD_DIR refer to). |
TOL |
= <tol_1 >, <tol_2 >, <tol_3 > |
Tolerances in the three axial directions for symmetrical recognition of
CLIENT = PLANE_SYM, POINT_SYM, ROTATION_SYM, SURF_STAMP, SURF_TURN, SURF_DRILL, SURF_PLANE_SYM,
SURF_CYCLIC_SYM, SURF_CYCLIC_PLANE_SYM or SURF_DEMOLD . |
Special Items for CLIENT Parameters
Not all entries are allowed for each parameter as shown in the following table:
|
SURF_STAMP |
SURF_TURN |
SURF_DRILL |
SURF_DEMOLD |
ROTATION_SYM |
SURF_CYCLIC_SYM |
SURF_CYCLIC_PLANE_SYM |
SURF_PARAM |
x (Ctrl only) |
x (Ctrl only) |
x |
- |
- |
- |
- |
SURF_SYM_TYPE |
x (Ctrl only) |
x (Ctrl only) |
x |
- |
- |
- |
- |
SURF_SYM_CS |
x (Ctrl only) |
x (Ctrl only) |
x |
- |
- |
- |
- |
SURF_SYM_NDGR |
x (Ctrl only) |
x (Ctrl only) |
x |
- |
- |
- |
- |
ANGLE |
x (Ctrl only) |
- |
x |
x |
x |
x |
x |
UNDERCUT_TOL |
- |
- |
x |
x |
- |
- |
- |
CHECK_GROUP |
- |
- |
- |
x |
- |
- |
- |
CYCLIC_SYM_START |
- |
- |
- |
- |
- |
x |
x |
MID_PLANE |
- |
- |
- |
x |
- |
- |
- |
IGNORE_ERRORS |
- |
- |
- |
x |
- |
- |
- |
REFERENCE_GEOMETRY |
x (Ctrl only) |
x (Ctrl only) |
- |
- |
- |
- |
- |
SURF_PARAM |
= <main_areas >, <net_points > |
Parameters for the surface algorithms with 4 < net_points < main_areas - 10%. |
SURF_SYM_TYPE |
= PLANE_SYM, AXIS_1
= PLANE_SYM, AXIS_2
= PLANE_SYM, AXIS_3 |
Plane symmetry linking for surfaces defined with the SURF_* parameters. |
|
= POINT_SYM |
Point symmetry linking for surfaces defined with the SURF_* parameters. |
SURF_SYM_CS |
= <name_of_cs > |
Name of the coordinate system for the SURF_SYM symmetry linking. |
SURF_SYM_NDGR |
= <name_of_nodegroup > |
Node group defining the main surface for a SURF_SYM definition. |
ANGLE |
= <real > |
|
|
= |
Draw angle for demold restriction at CLIENT = SURF_STAMP , SURF_DRILL , SURF_DEMOLD . |
|
= |
Angle for the repeating segments at CLIENT = ROTATION_SYM , SURF_CYCLIC_SYM , SURF_CYCLIC_PLANE_SYM . |
|
= 0 |
If the nodes are rotational symmetric but not in a periodical order
at CLIENT = ROTATION_SYM , SURF_CYCLIC_SYM ,
SURF_CYCLIC_PLANE_SYM . |
UNDERCUT_TOL |
= <real > |
Measure > 0 for tolerable undercut in the demolding area. |
CHECK_GROUP |
= <name_of_node_group > |
Name of the check group for the demold definition. |
CYCLIC_SYM_START |
= <x_1 >, <x_2 >, <x_3 > |
Defines the starting point for the partitioning. Its coordinates are given with reference to the global Cartesian coordinate system.
It must not lie on the rotational axis. |
MID_PLANE |
= POINT, <x_1 >, <x_2 >, <x_3 > |
A point within the central plane from which the deformation vector is positioned perpendicular to. |
IGNORE_ERRORS |
= YES, NO |
The demold control checks for undercuts in the start model and stops if any undercut is found. Set this option to YES to ignore this error. |
REFERENCE_GEOMETRY |
= CURRENT, INITIAL |
Determines which geometry is used to determine the dependencies between the nodes.
In case of CURRENT , the geometry with applied optimization displacements is used.
For INITIAL , the geometry from the beginning of the optimization is used. |
Remarks
- The allocation is only permitted for design nodes (defined by the command
DV_SHAPE ) and mesh smooth nodes (second order design nodes).
- The
MAIN specification determines the main nodes.
|
Case 1 |
Case 2 |
Case 3 |
Case 4 |
|
ALL_GROWTH
|
ALL_SHRINK
|
MORE_SHRINK
|
MORE_GROWTH
|
|
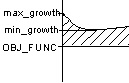
|
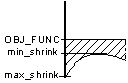
|
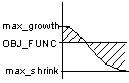
|
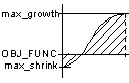
|
MAIN
|
Selected Main Displacement Value |
MAX
|
max_growth |
min_shrink |
max_growth |
max_growth |
MIN
|
min_growth |
max_shrink |
max_shrink |
max_shrink |
- The
CLIENT specification determines the displacement of the client nodes from the main_Node of the optimization displacement.
CLIENT = PLANE_SYM : The surface that lies normal to the specified axis is a symmetrical surface.
The nodes (allocated by DVCON_SHAPE operator ND_GROUP ) are checked against each
other for their symmetry and symmetrical surfaces. Symmetrical nodes are combined to a symmetrical group
(2 symmetrical nodes per symmetrical group is the norm). The main node of the symmetrical group is then determined and
the displacement of the client node is calculated so it displaces in a surface symmetrical fashion to the main node.
CLIENT = POINT_SYM : The point defined by the origin of the coordinate system CS is called the symmetrical point.
The nodes (allocated by DVCON_SHAPE operator ND_GROUP ) are checked against each other for
their symmetry with reference to the symmetrical point. Symmetrical nodes are combined to a symmetrical group (2 symmetrical
nodes per symmetrical group is the norm). The main node of the symmetrical group is then determined and the displacement of
the client node is calculated so it displaces point symmetrical to the main node. For both symmetrical couplings the given
coordinate system in the operator CS must be Cartesian (rectangular). The operator MAIN
must have MAX or MIN .
CLIENT = ROTATION_SYM : The specified axis defines the rotation axis of the surface of revolution. The nodes
(allocated by DVCON_SHAPE operator ND_GROUP ) are checked for their symmetry in the given
rotation axis. All nodes at the same parallel of the surface of revolution are combined to a symmetrical group. The main
node of the symmetrical group is then determined and the displacement of the client node is calculated so it displaces in a
surface symmetrical fashion to the main node.
CLIENT = VECTOR : Referring to the coordinate system entered in the operator CS , the difference
between the current coordinates and the start coordinates of the main nodes is calculated. With reference to the coordinate
system the start coordinates of the client nodes are then calculated, the difference in the main nodes are determined and the
current coordinates of the client nodes are calculated. With VECTOR =ON /OFF ,
ON /OFF , ON /OFF these coordinates are activated and transferred.
The coordinates deactivated remain unchanged.
CLIENT = DIRECTION : The procedure is similar to that of CLIENT = VECTOR with coupling of all
three coordinates. The difference is that the obtained displacement vector is scaled to the original absolute value of the displacement of the client node.
CLIENT = LENGTH : The absolute value of displacement of the main nodes is calculated. The displacement of
the client nodes is scaled so the absolute value of the obtained displacement of the main node remains.
CLIENT = DISP_CS : The optimization displacement of the main nodes based upon the FE displacement coordinate
system is transferred directly in the FE displacement coordinate system of the client nodes. The coupled FE displacement
coordinate systems must be of the same kind, that is, either Cartesian, cylindrical, or spherical. With
DISP_CS=ON/OFF, ON/OFF, ON/OFF these coordinates that are activated are transferred. The coordinates deactivated remain unchanged.
CLIENT = SURF_PLANE_SYM : The nodes are checked to be symmetric with respect to the given symmetry plane in
symmetric but nonsymmetric meshed models. The node corrections are applied in node normal direction only.
CLIENT = SURF_CYCLIC_SYM : Couples nodes in a not necessary symmetric mesh that reoccur in a cyclic manner around a rotational axis.
CLIENT = SURF_CYCLIC_PLANE_SYM : Combination of SURF_CYCLIC_SYM and SURF_PLANE_SYM .
Nodes are first coupled in a cyclic manner and then plane symmetry is enforced within each cyclic section. The position of the plane
symmetric sections is controlled with the CYCLIC_SYM_START parameter.
CLIENT = SURF_STAMP :
- The nodes are linked to keep a stampable surface. main nodes are determined automatically.
- The main options
MAX and MIN are not permitted for sensitivity-based optimizations.
CLIENT = SURF_TURN :
- The nodes are linked to keep a turnable surface. main nodes are determined automatically.
- The main options
MAX and MIN are not permitted for sensitivity-based optimizations.
CLIENT = SURF_DRILL : The nodes are linked to keep a turnable surface.
main nodes are determined automatically. The drill restriction is a special combination of the turn and demold restriction.
CLIENT = SURF_DEMOLD : The nodes are linked to keep a castable surface.
- The
CLIENT s PLANE_SYM , ROTATION_SYM , SURF_STAMP ,
SURF_TURN , SURF_DRILL , SURF_DEMOLD , SURF_CYCLIC_SYM ,
SURF_PLANE_SYM , SURF_CYCLIC_PLANE_SYM can be used without the AXIS_*
parameter. Thus, an arbitrary axis direction <x,y,z> can be specified with reference to CS with
the entry CLIENT_DIR = x,y,z . For SURF_STAMP an additional demolding direction can be
defined using the DEMOLD_DIR parameter, also available for the definition of the demolding direction for SURF_DEMOLD .
CS : Name of the coordinate system that
operates LINK_SHAPE . Specifying the coordinate system is essential for
CLIENT =PLANE_SYM , POINT_SYM ,
ROTATION_SYM , VECTOR , DIRECTION ,
SURF_STAMP , SURF_TURN , SURF_DRILL ,
SURF_DEMOLD , SURF_CYCLIC_SYM ,
SURF_PLANE_SYM , or SURF_CYCLIC_PLANE_SYM . Specifying the
coordinate system for CLIENT =LENGTH , or
DISP_CS is unnecessary. With
CLIENT =PLANE_SYM and POINT_SYM only
Cartesian coordinate systems are permitted.
TOL : Specifying the tolerance values
for CLIENT =PLANE_SYM , POINT_SYM ,
ROTATION_SYM or SURF_DEMOLD is essential. Specifying the
tolerance values for CLIENT =VECTOR ,
DIRECTION , LENGTH , DISP_CS ,
SURF_STAMP , SURF_TURN , SURF_DRILL ,
SURF_CYCLIC_SYM , SURF_PLANE_SYM , or
SURF_CYCLIC_PLANE_SYM is unnecessary. The tolerance values must be positive.
At least one of three tolerance values must be entered. For tolerance values not given, the
smallest of the given tolerance values is acceptable. The three tolerance values are also
coordinate values referring to the three coordinate directions of the CS . The
values of tolerance should be large enough to cover the individual nodes and small enough not
to cover any not wanted neighboring nodes.
- The parameter
SURF_PARAM = <main_areas>, <net_points> is used to create a spline that defines the
"surface" in the allowed LINK_SHAPE commands. The values
<master_areas >, <net_points > are integer values
and automatically determined by Tosca Structure.
In the event of an error, it might help setting SURF_PARAM . Important is
that <master_areas > must be larger than 4 and at least double the size
of <net_points >. Good values are, for example, SURF_PARAM = 12, 4 .
Examples
LINK_SHAPE
ID_NAME = my_link_01
MAIN = MAX
CLIENT = PLANE_SYM, AXIS_3
CS = cs_0
TOL = 0.01, 0.01, 0.01
END_
LINK_SHAPE
ID_NAME = DEMOLD_AREA
MAin = MAX
CLIENT = SURF_DEMOLD, AXIS_2
CS = cs_0
ANGLE = 1.5
TOL = 0.01, 0.01, 0.01
CHECK_GROUP = CHK_NDGRP_DEMOLD
END_
|